In our decades of experience shipping thousands of tons of freight, we discovered one simple task that reduces freight costs for our clients. In the same way that we reconcile bank balances, we reconcile all our shipping bills every month. It typically saves us hundreds of dollars per month.
This recent story illustrates how these surprise freight charges happen and what you can do to minimize shipping costs.
Examples of Questionable Freight Charges
We shipped out two skids packed and wrapped as shown in the photo below.
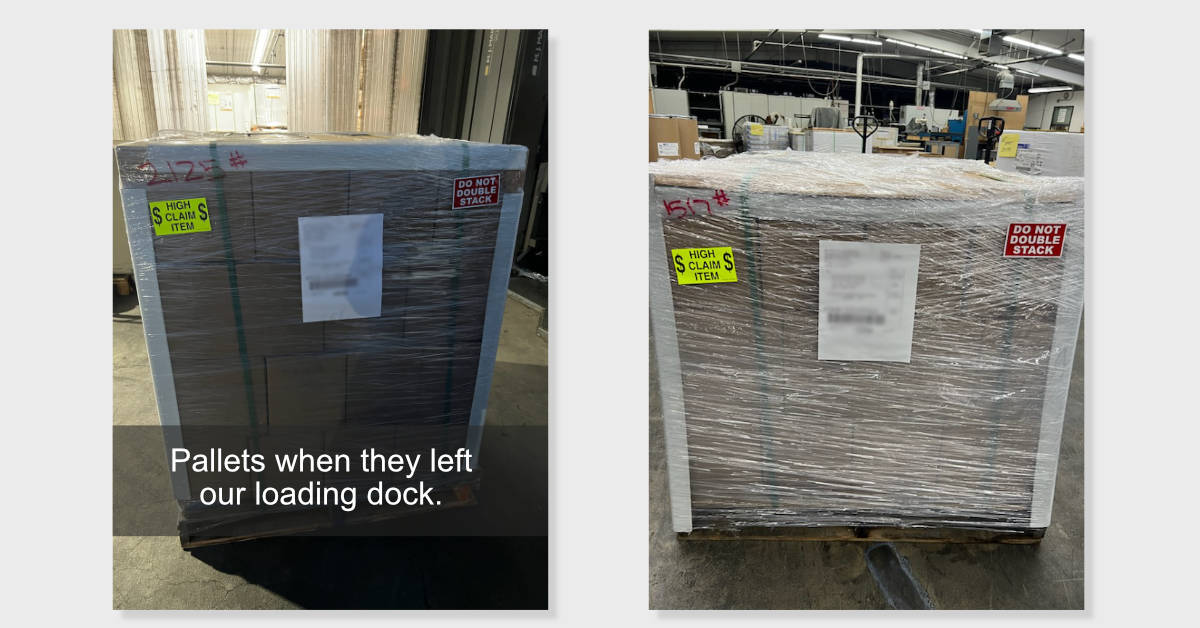
All our skid shipments are extremely well protected with corner protectors, heavy duty strapping, and stretch wrap. We also photograph every shipment. (You can read more about our ground and LTL shipping methods here.)
The shipment arrived as shown here.
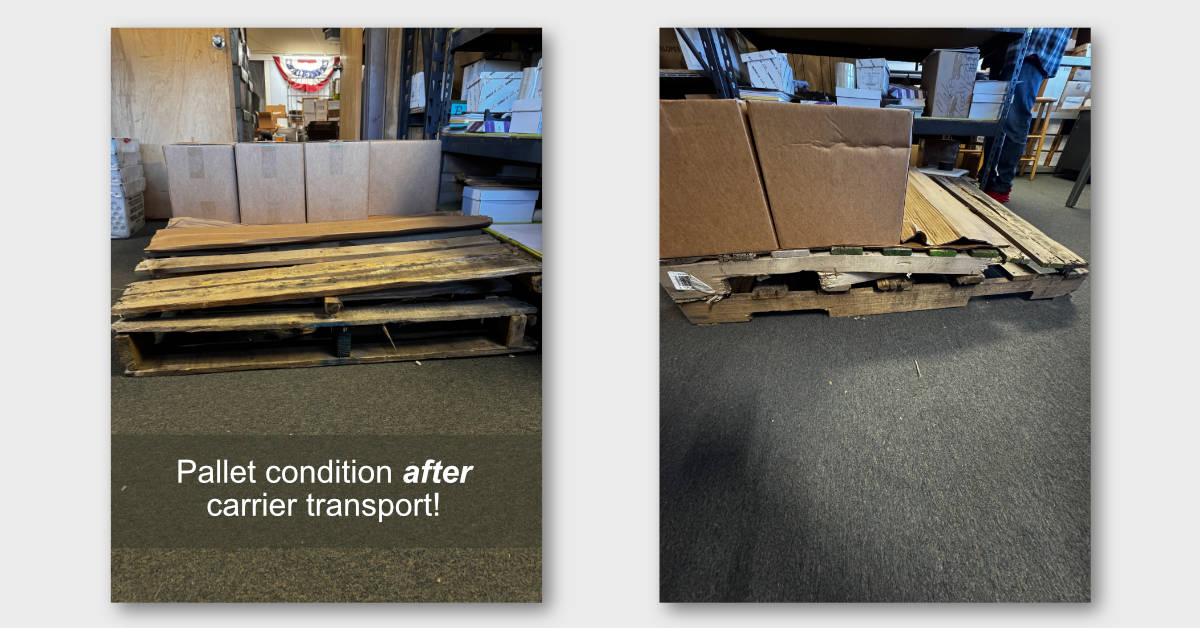
The carrier team did their best to get the goods delivered to the consignee in as good condition as possible. When the truck arrived, they could not get a pallet jack under the load to offload. It took 47 minutes to get this unloaded because the consignee and the driver had to "drag" the load to the back of the truck and offload by hand.
To their credit, the team put in a lot of effort and the goods were delivered intact, with superficial damage only to the boxes.
Here is the problem – the carrier invoiced us $135.00 for "wait time" for something that clearly happened on their watch. The wait time was undoubtedly due to their negligence.
When questioned, they reversed the charge.
Here’s another common but questionable practice we found that inflates shipping costs.
We’ll schedule a “dock to dock” shipment. We load the truck on our dock and the consignee unloads on their dock. But this is what happens. The driver shows up with a liftgate truck and offers to use the liftgate. The consignee says, “Sure!” because it sounds like a courtesy. Then we get charged additionally for the liftgate service even though it wasn’t ordered, requested, or needed. It’s a sneaky way for the carrier to tack on a significant charge. A phone call gets the charge reversed.
Results of Shipping Invoice Reconciliation
Here at WTP, we challenge about 10% of our shipping invoices when they add "rebills". There is never any communication from the freight company about these extra charges, they just add it to the invoice. I suspect that a HUGE percentage of these are never questioned because the accounting department has no clue what is truly happening. They just see a shipping invoice from a regular supplier and pay the bill.
For years we were blindly over-paying as much as $500.00 per month among a half dozen carriers who were all adding illegitimate upcharges. Over 90% of the invoices we challenge get corrected! Many of these charges are most likely computer-generated. As in the first example, the truck is likely to have a GPS tracker. They can see how long the driver was there, so their system automatically adds the additional “wait time” charges.
The Simple Way to Quickly Decrease Shipping Costs
The bottom line—reconcile all freight bills monthly. The amount of time it takes to reconcile shipping invoices is almost certain to result in substantial reductions in billing. It’s a simple administrative task that will more than pay for the time involved.